Couler son lest
N’étant pas satisfait de mon lest, car je le trouve trop angulé, je me suis lancé dans la fabrication d’un nouveau lest.
Mon premier essai n’a pas été une réussite, car les cheminées que j’avais faites aux extrêmités du moule n’étaient pas suffisamment larges et le plomp a refroidi et bouché les issues. Des poches d’air se sont formées et le plomb n’a pas coulé vers les extrêmités de façon satisfaisante.
La seconde raison est que j’ai fait le coulage dehors, par temps froid (0°C), et que je n’ai pas assez chauffé le moule avant l’opération.
Mais un échec, c’est une occasion d’apprendre, pas vrai ?
Alors voici une méthode qui permet de fabriquer son moule et de couler un lest aux dimensions voulues, avec le poids cible souhaité.
Il y a plusieurs méthodes, celle présentée donne une idée des étapes pour confectionner quelques lests de façon occasionnelle. Le recours à un moule en fonte est plus appropriée pour de la série, mais c’est rarement notre cas en modèlisme.
L’idée est de concevoir le moule en utilisant un logiciel CAD. L’avantage est de pouvoir choisir la forme que l’on veut, en prévoir les orifices pour les vis de fixation et le sabot de la dérive et d’en connaître le volume final de la forme – ce qui en donne le poids final.
Pour cela, il y a plusieurs solutions :
– En ligne le logiciel ;
– ONSHAPE
– sur son poste :
– FreeCAD
– Rhino7
– bulbcalc (http://b10rrrrrrrrrrrrrrrrrrrrrrrrrrrrrrrrr.e-monsite.com/pages/technique-appendices/test-1-1.html)
– etc.
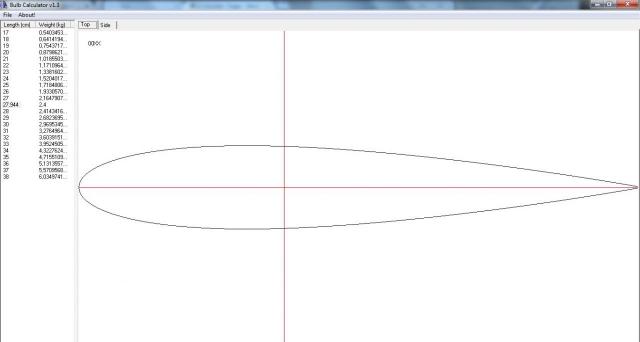
L’exemple décrit ici est fait avec Rhino7. Ce logiciel permet de concevoir son lest, d’y placer ses inserts et de produire un fichier .stl qui va permettre d’imprimer deux demi-matrices du lest que l’on veut faire à l’imprimante 3D. Il possède une fonction qui permet de connaître le volume et le poids si on prend la densité du plomb et c’est très pratique. Le logiciel bulbcalc permet aussi de créer un plan pour un lest dont on a choisi la masse également (le poids) ainsi que la forme (le profil NACA).
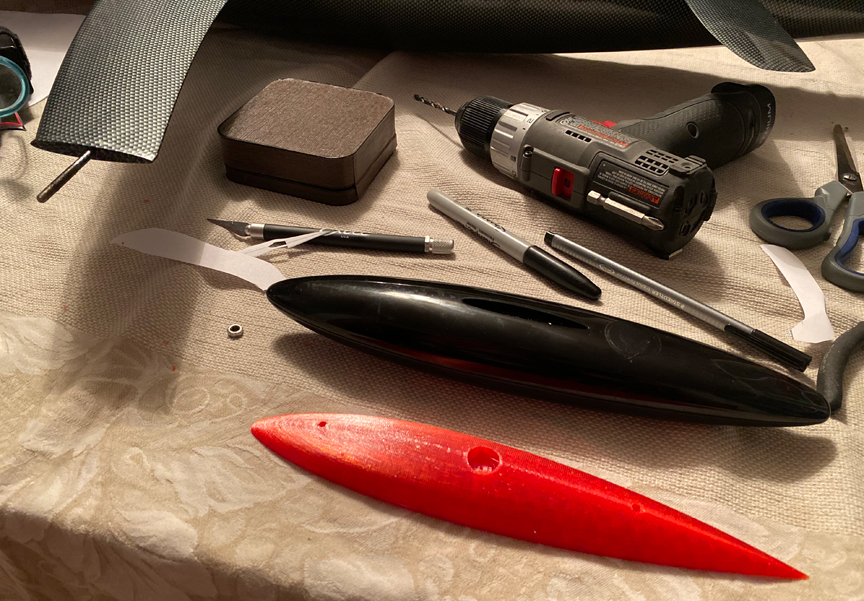
Avec ces deux demi-matrices, on va pouvoir vérifier le positionnement sur la dérive et l’emplacement idéal du point de fixation du futur moule au pied de la dérive et si besoin le corriger. Evidemment cette vérification faite avec un modèle très léger a un intérêt limité à l’ajustement de l’assemblage lest/dérive et éventuellement à l’inclinaison du lest relativement à la ligne de flotaison, mais pas plus.
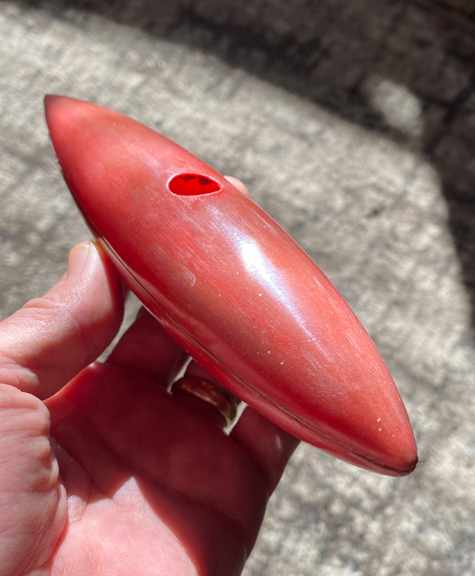
Chaque demi matrice va permettre de fabriquer le moule en deux parties.
Pour cela on va fabriquer une boîte qui va servir au moulage de l’ensemble. Le fond de la boîte va recevoir la demie-matrice à mouler.
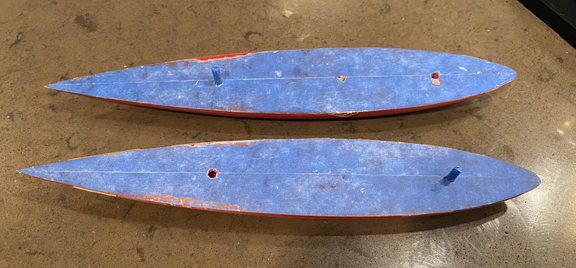
Dans l’exemple illustré avec les photos, la demie matrice étant fixée au socle, est recouverte de silicone. Il faut utiliser un silicone qui résiste à la température de fusion du plomb évidemment. On en trouve notamment sur des sites en ligne. Ce silicone est connu sous le nom de silicone rouge.
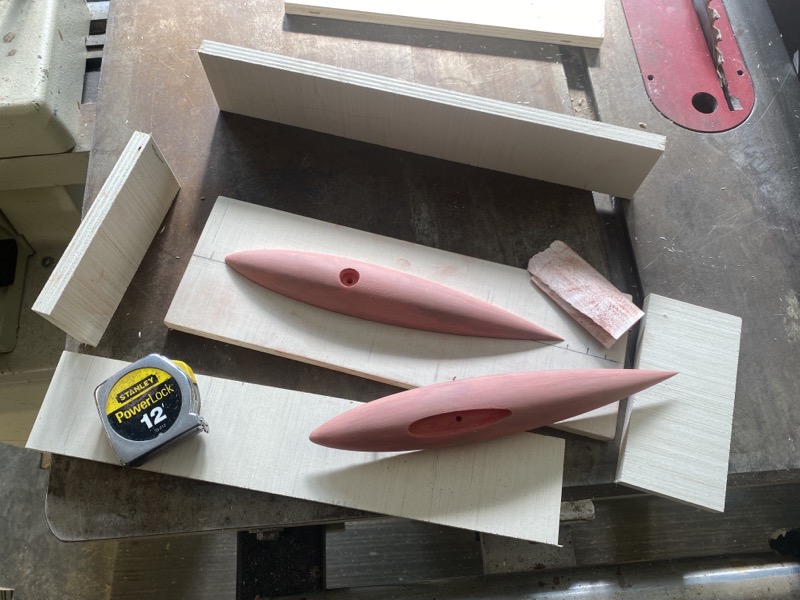
Le silicone étant enduit et sec, on coule du platre pour servir de socle solide au futur moule.
Les deux demi moules étant faits, on les assemble.

Pour mon premier, moule, je n’avais pas de silicone, alors j’ai enduit le moule d’huile et coulé le plâtre par-dessus la matrice et cela permet un démoulage très facile. J’ai également utilisé de l’huile pour badigeonner le premier moule de façon que le second que l’on coule par-dessus, se démoule facilement.
Des plots de calage sont créés, ici avec des demies sphères posées au quatre coins. Au moulage du second demi-moule, le plâtre viendra remplir les cavités sphériques. Ce qui va permettre de toujours repositionner parfaitement les deux demi moules.
On prévoit les cheminées d’évacuation des vapeurs au moment de la coulée du plomb. Il faut deux cheminées aux deux extrêmités et deux au milieu sur la partie supérieure du lest au moment de la coulée du plomb. Sans quoi, des poches d’air se forment et le coulage est à refaire ! (Là je parle d’expérience…)
Il faut un diamètre suffisant pour les cheminées. A mon premier essai j’avais utilisé une mèche de 3 mm pour faire les cheminées et ce diamètre ne s’est pas avéré suffisant.
A noter que la fabrication de moules dont les moitiés sont coulées séparement puis que l’on assemble ensuite à la colle epoxy évite ce problème – mais celà est remplacé par du ponçage.
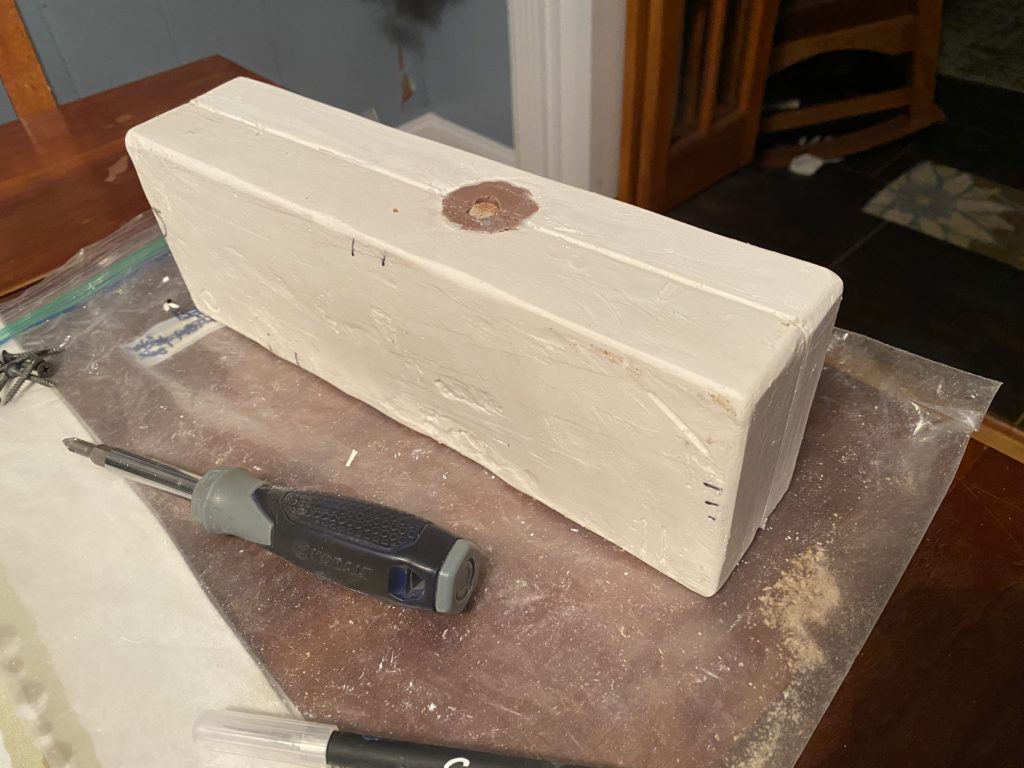
Pour préparer le moule avant la coulée, l’utilisation du talc est recommandée – le talc obstrue les moindres petits trous et il protège le moule (en silicone ici, ou en platre si on a pas utilisé de silicone). Par exemple un moule en plâtre, s’il est talqué, gardera un bel aspect de surface après le démoulage – permettant de le ré-utiliser.
Ici, j’ai placé au milieu du moule à l’assemblage une tige de 4 mm qui fait la longueur du lest. Je l’ai limée pour obtenir un bord de fuite affiné. Cette tige a l’avantage de raidir le lest final qui est moins sensible aux chocs et restera plus facilement bien aligné. J’ai utilisé de l’aluminium car je n’avais rien d’autre sous la main – mais le laiton c’est bien mieux, car cela ne s’oxyde pas.
Avant la coulée, il faut faire sécher le moule plusieurs jours, surtout si on n’a pas utilisé de silicone.
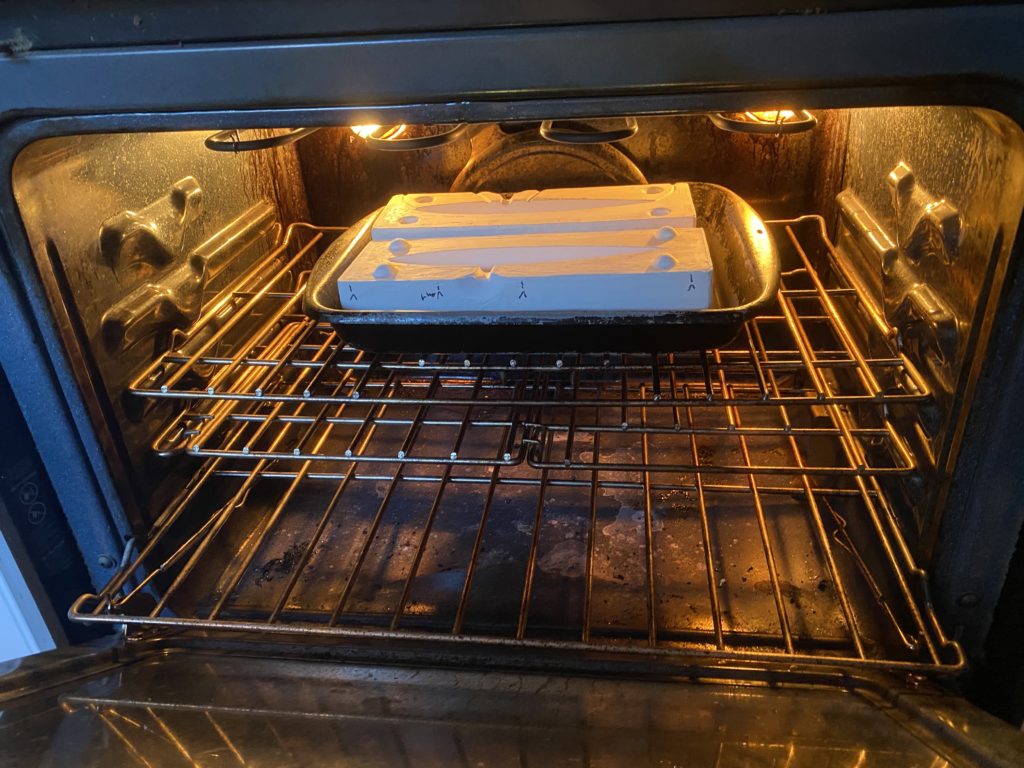
Et dans la période qui précède la coulée, on le préchauffe au four pendant trois quart d’heure à 50 °C environ. La coulé dans un moule chaud donnera un bien meilleur résultat en évitant que le plomb fondu ne se fige avant d’avoir entièrement occupé la cavité du moule.
Le moule étant prêt, on le ferme. Il faut bien vérrouillé les deux parties ensemble pour que cela ne bouge pas sous la pression du plomb fondu.
On fait fondre le plomb et on le coule dans le moule.
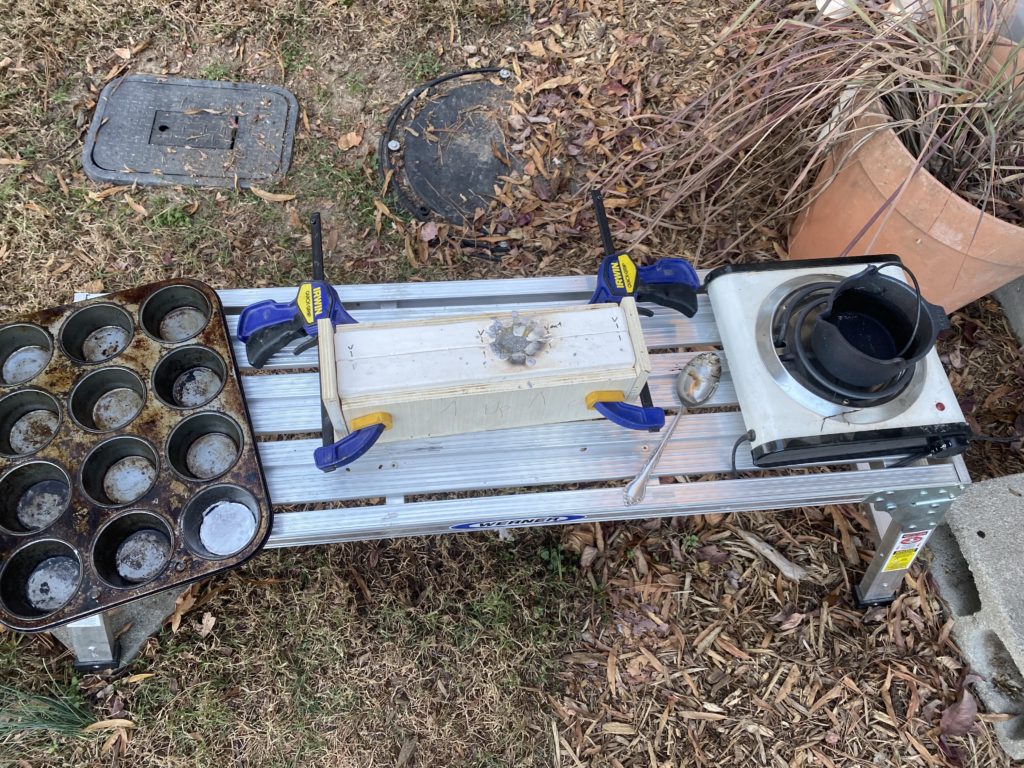
Une fois le plomb refroidi, ce qui peut prendre du temps car il est bien au chaud au milieu du moule (cela a bien pris deux heures dans mon cas), on peut procéder au démoulage.
Pour cela on dévérouille les deux parties et on écarte les deux moitiés tout autour de l’assemblage.
Normalement cela vient facilement, surtout si on a utilisé du talc.
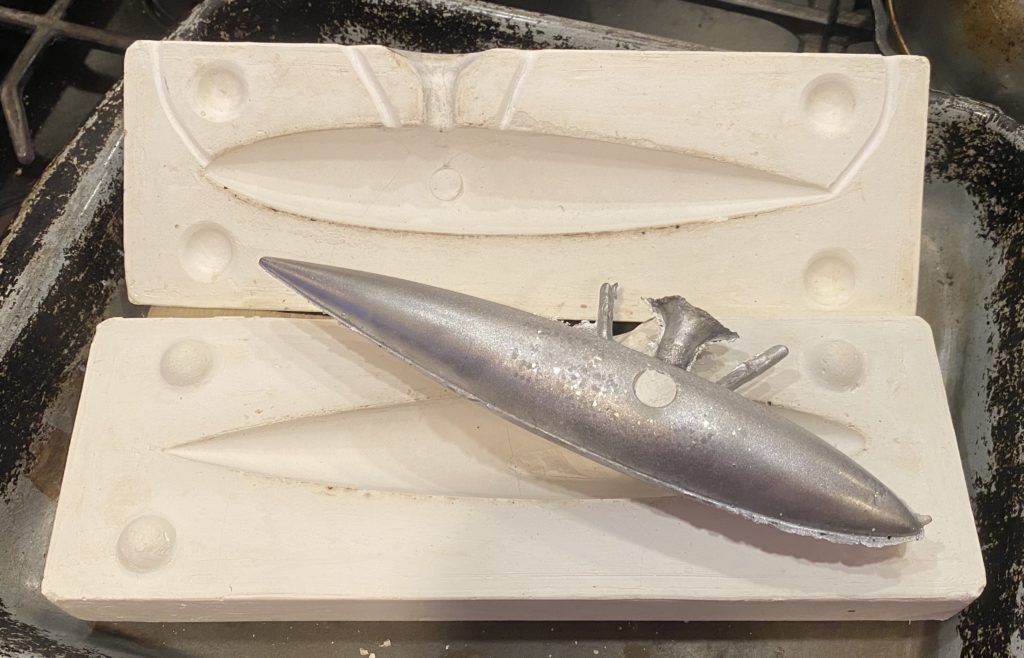
Le lest brut doit être débarassé des barbes qui l’entoure et les excroissances des cheminées qui se sont remplies de plomb. Cela se fait au cutter et à la lime.
Le lest brut est alors enduit au mastic polyester qui une fois sec est soigneusement poncé.
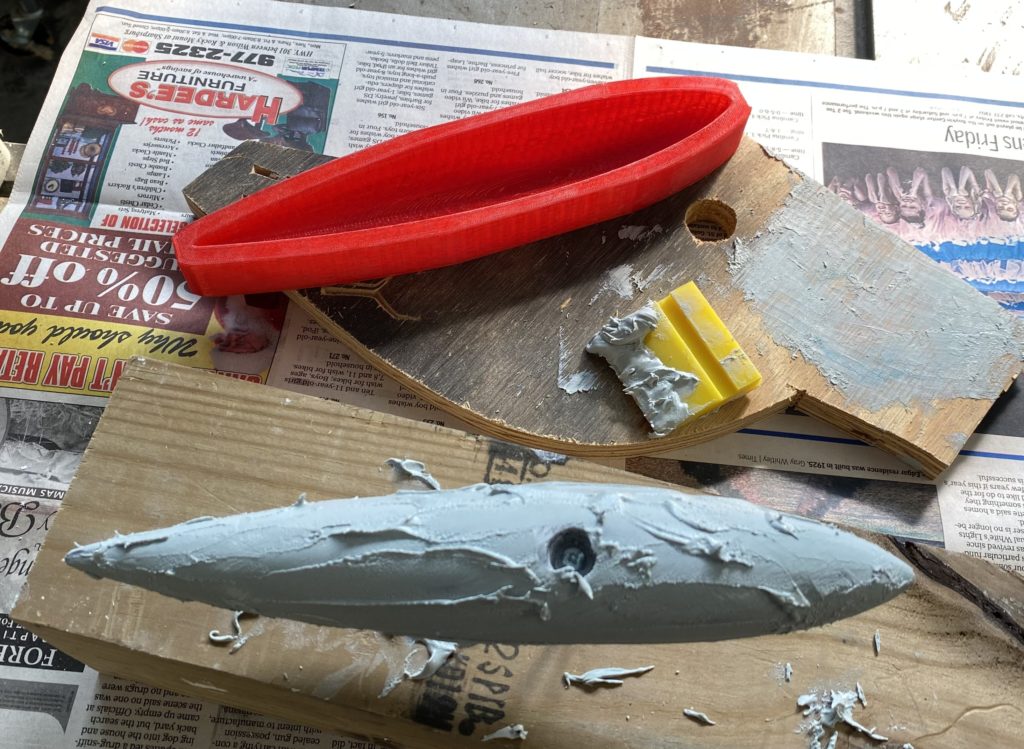
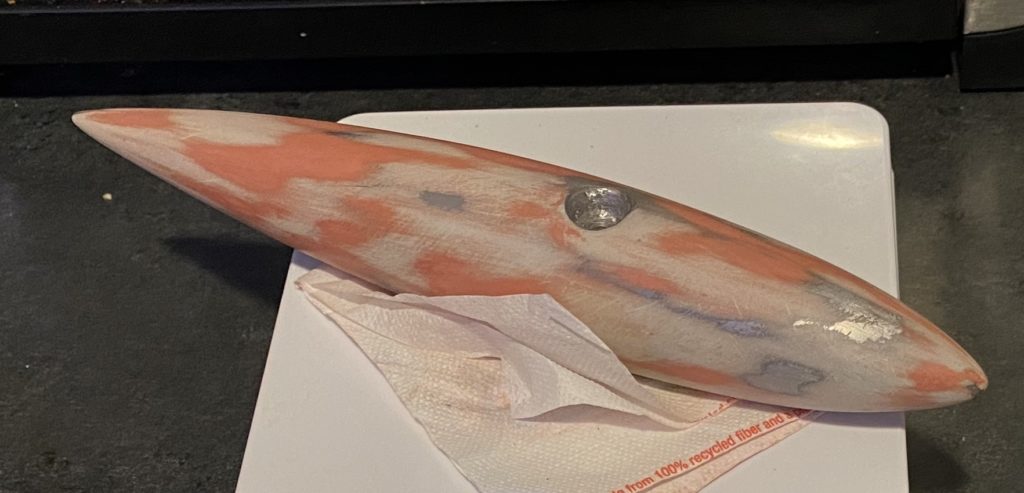
Enfin on recouvre le lest d’une sous-couche, puis d’une peinture dure passée au pistolet.
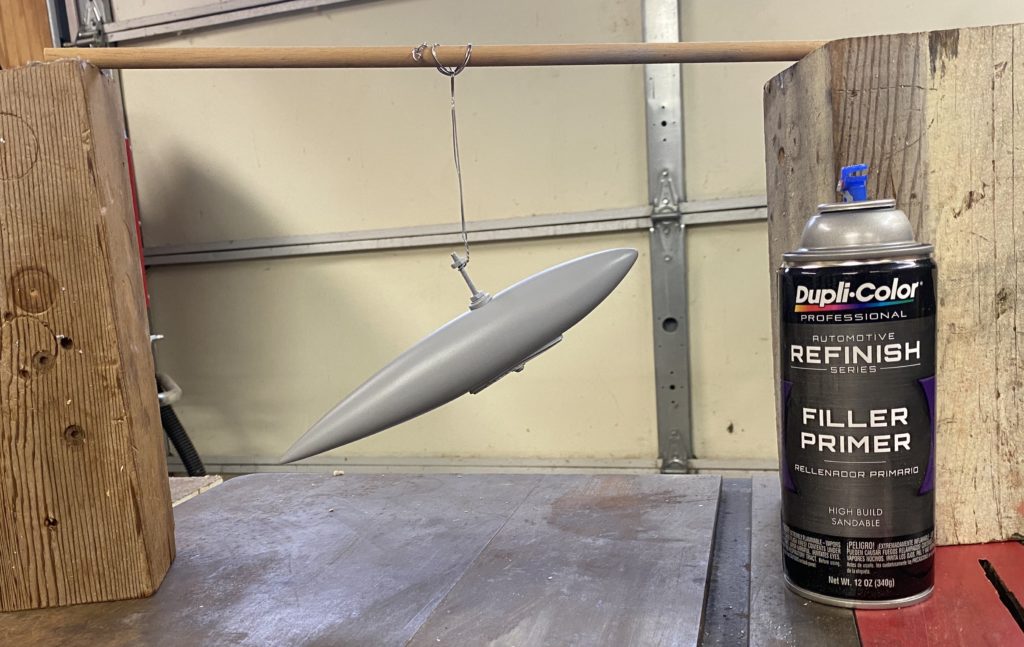
Le lest est prêt pour l’assemblage à la dérive.
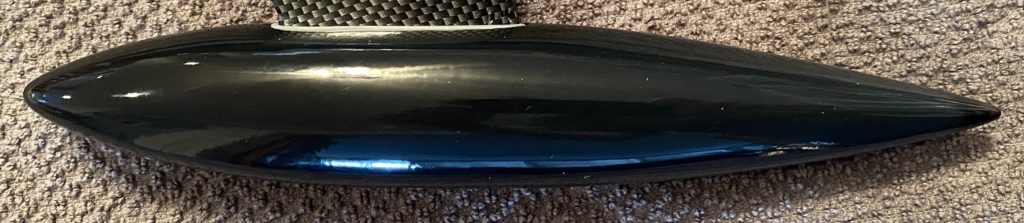
Cette opération est très délicate car il faut absolument que le lest soit parfaitement alignée avec l’axe du bateau et qu’il soit légèrement incliné vers le haut pour compenser la tendance du bateau à plonger le nez au portant. L’angle le plus couramment utilisé est de 2°4
On peut mettre moins dans les petits airs mais cette valeur est un bon compromis.
Un angle plus grand freine le bateau, comme je l’ai constaté sur mon bateau !

Championnat de Bretagne 2022
Compte-rendu de l'AG de l'AFCM 2019
Vous aimerez aussi
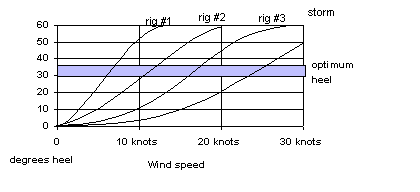
Choix du bon gréement pour le vent du jour
15 février 2022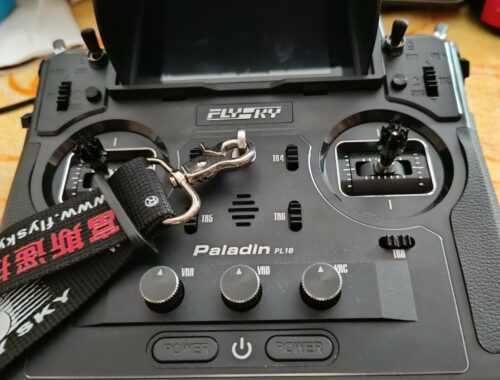
Parlons « Flysky » !
1 mai 2024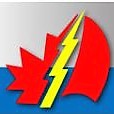